Moulding plays a crucial role in the manufacturing industry, as it allows for the production of a wide range of components. However, even the most sophisticated moulding processes can be prone to defects that compromise the quality of the finished product. In this article we will explore the importance of defect analysis in moulding and how this practice can help to achieve better performance.
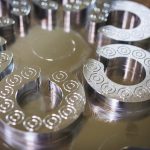
1- Identification of the most common defects
Defects in moulding can have different shapes, including air marks, deformations, embrittlement, tears, and more. These defects can be caused by a few factors, including design errors, temperature and pressure variations, contamination in the compound used, imperfections in the alignment of the press, to name a few.
To identify and analyse defects in moulding, a few tools and techniques must be used. These can include visual inspections, microscopic analysis, testing on the moulded article, and more. The combined use of these methods makes it possible to accurately identify the causes of defects and take appropriate corrective measures.
2- Process optimization
To improve moulding performance, it is essential to optimize process parameters and select the most suitable materials. In the optimization of moulding processes, a crucial element is the choice of mould. Selecting the right type of steel and applying the appropriate surface treatments can have a significant impact on moulding performance.
The choice of steel for the mould depends on the specific needs of the moulding process, including factors such as working temperature and pressure, production frequency, and the complexity of the rubber article to be produced. Steels with high wear and corrosion resistance properties are often preferred to ensure the durability of the mould and the quality of the finished part over time.
In addition, the application of surface treatments such as polished or satin chrome plating can further improve the performance of the moulding. This treatment can reduce wear and corrosion and improve resistance to mechanical stress, thus helping to extend the service life of the mould and ensure repeatability of the moulding process.
The key step of choosing the right mould and surface treatments is therefore crucial to ensure the quality and performance of the moulding process, while reducing production and maintenance costs in the long-term period.
3- Practical example
1 – A customer who moulded a rubber bellows had a 32% scrap rate on the moulded parts, caused by the article tearing during detachment.
He turned to us to understand the cause of this defect. We satin and chrome-plated the mould, and now the piece detaches very easily and the % of waste has dropped from 32% to 4%
2 – Another customer had a problem of imperfections on the joint of the moulded piece, at the point opposite to the rubber inlet. He turned to us for help. We thoroughly analyzed the mould (not produced by us) and found that the cause was an inadequate processing of the air vent. We therefore modified the air vents, making them more consistent and more effective in their usefulness. Air venting, in fact, is a very important process that allows you to make a difference in the quality and uniformity of moulded pieces.
In conclusion, the analysis of defects in moulding is a fundamental process to ensure the quality of technical rubber items. Through the precise identification of defects and the implementation of appropriate corrective measures, significant improvements can be achieved in the moulding phase of technical rubber or O-Ring articles. However, it is important to remember that process optimization is an ongoing activity and that constant research and development are essential to meet future challenges in the moulding industry.