The importance of quality control in the production of moulds for technical rubber articles
In the mould manufacturing industry, quality control is a crucial aspect to ensure accuracy and reliability. OCS stands out for its rigorous approach thanks to an actual office dedicated to quality control, an element that many other companies in the sector do not have. Our goal is to ensure that no non-conforming mould leaves the production site. In an ever-changing landscape, new technologies are transforming quality control processes, enabling greater efficiency and accuracy in verifying mould characteristics.
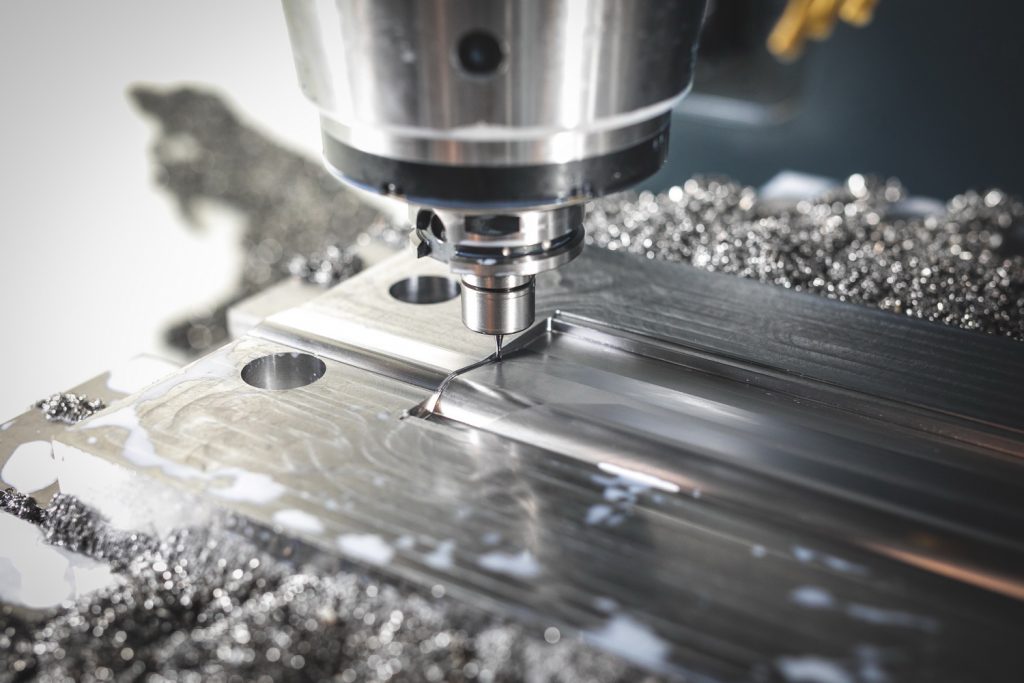
Quality control is a fundamental process that involves a series of steps aimed at ensuring that each mould for technical rubber articles meets the required technical specifications and tolerances. At OCS, quality control is divided into different levels of verification:
- Visual inspection: a preliminary examination that allows to identify any macroscopic defects.
- Basic instrument testing: using tools such as micrometers, calipers, and dial gauges for precise measurements of dimensions and tolerances.
- Optical machine/microscope check: an essential step in detecting microscopic imperfections that would escape a simple visual inspection.
- Inspection with Zeiss measuring machine: mainly applied to moulds for OR (O-Rings) and similar, this inspection ensures extreme precision in three-dimensional measurements.
The purpose of quality control is to ensure that the moulds are within specifications and meet tolerances, thus ensuring high performance during moulding. Strict quality control allows OCS to provide ready-to-use moulds, reducing the risk of returns and optimizing production times for customers.
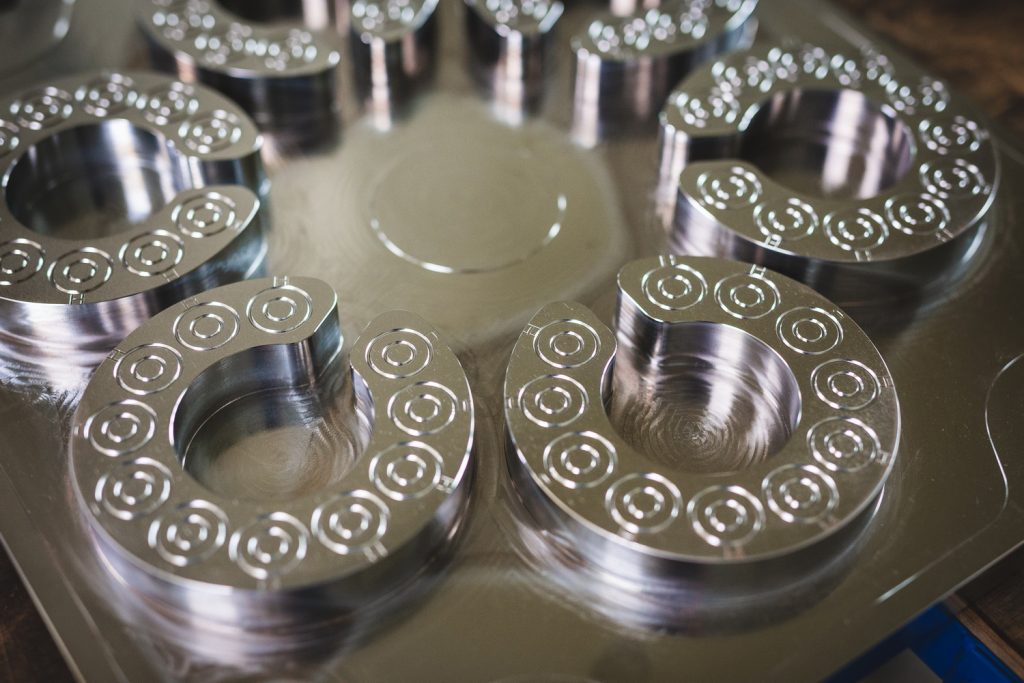
New technologies in quality control
Emerging technologies are revolutionizing the quality control process, bringing significant innovations in measurement and analysis. Here are some of the key technologies:
- 3D measuring systems: these tools provide a precise and detailed three-dimensional view of the moulds, allowing the exact dimensions and overall geometry to be determined.
- Automated inspection: Zeiss measurement technology enables advanced detail analysis, delivering reliable and consistent results.
Benefits of automation in quality control
The introduction of advanced technologies in the quality control process brings numerous advantages, including:
- Speed and accuracy in processes: the use of automated tools speeds up the verification process, ensuring consistent accuracy and minimizing human error.
- Reduction of sunk costs for the customer: automation, thanks to the efficiency of processes, allows to guarantee greater precision and reduce the costs related to the correction of defects and returns.
- Continuous monitoring and efficiency improvement: advanced systems provide constant control of measurements, driving continuous process improvement and ensuring compliance with technical specifications.
Quality control is a fundamental to ensure the precision and reliability of the moulds, an aspect that today more than ever benefits from the integration of new technologies. Investing in advanced tools, such as three-dimensional measurement systems and optical controls, is not only a competitive advantage, but a necessity to maintain high standards and respond effectively to market needs. In a sector where precision is synonymous with performance, the continuous improvement of quality control processes allows customer companies to mould high-quality technical rubber articles, minimizing the risk of defects and waste of raw material.