Mould deterioration is a common issue in the rubber and elastomer industry, affecting the quality of moulded parts and increasing maintenance costs. Identifying the main causes of mould wear is essential to reduce moulding defects and extend the mould’s lifespan.
Typical defects caused by wear
One of the most noticeable effects of wear is the appearance of burrs in the mould. This results in excessive flash on technical rubber components, compromising the quality of the final product. When a mould becomes worn, the closure between its parts is no longer perfect, causing surface defects that are difficult to eliminate.
Another frequent issue is the difficulty of deflashing. If the injection gate area is too worn, the excess material flash increases, making the deflashing process more complex. This not only affects productivity but can also lead to high scrap rates and additional finishing costs.
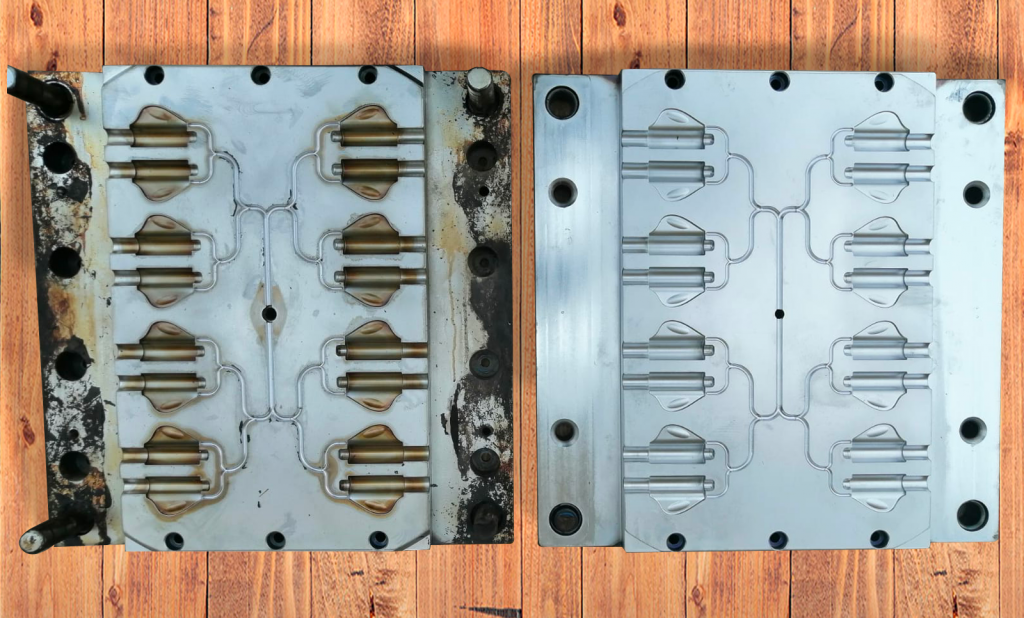
Main causes of mould deterioration
Mould deterioration depends on several factors, which can be divided into two categories:
1. Mould-related factors
- Type of steel used – Lower-quality materials tend to wear out more quickly.
- Applied treatment – Inadequate heat treatments or coatings can reduce wear resistance.
- Part geometry – Complex shapes or fine details can increase the risk of deterioration.
- Technology used (injection or compression moulding) – The choice of moulding process influences the pressure and mechanical stress applied to the mould.
2. Type of elastomer used
Not all elastomers are the same – some materials are more abrasive than others, accelerating mould wear. The ranking of elastomers from most to least abrasive is as follows:
- Silicone (highest abrasiveness)
- All light-filled and coloured compounds
- HNBR
- Viton
- Vamac
- EPDM
- ACM
- Neoprene
- NBR (lowest abrasiveness)
To minimise mould wear and improve product quality, it is essential to select durable materials, appropriate treatments, and efficient moulding technologies. Relying on the expertise of the mould maker is crucial. Additionally, understanding the characteristics of the elastomer being used, particularly its level of abrasiveness, helps prevent premature mould deterioration.
Through proper maintenance and strategic decisions at the initial design phase, it is possible to optimise mould longevity and reduce production costs. Strong collaboration and communication between the customer and supplier are therefore key to achieving superior quality results.