We study and realize the best solutions for every type of mold, optimizing planning and construction techniques while experimenting new ones to enhance their use and duration in time as well as reducing to the minimum raw material waste.
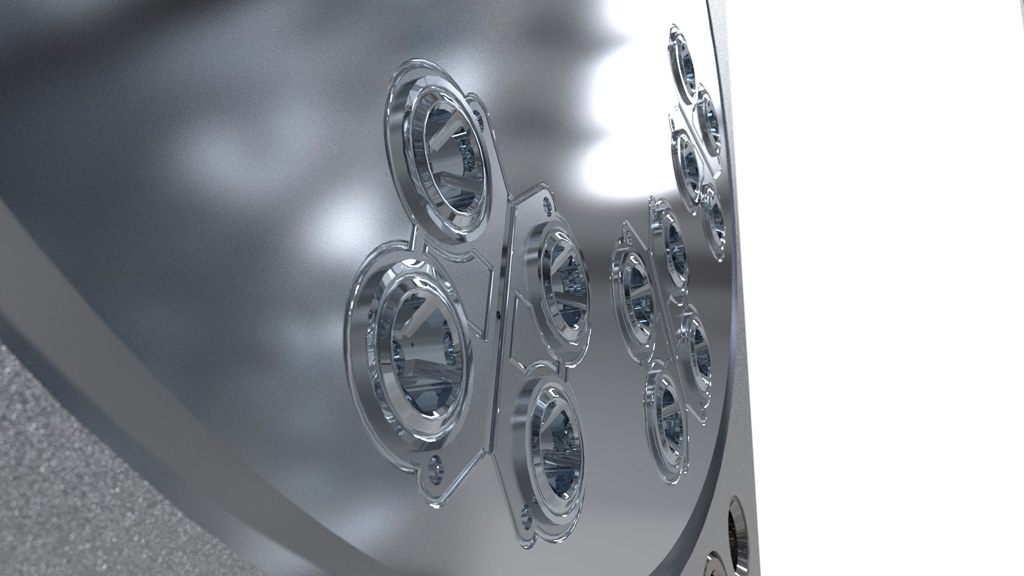
CLOSED INJECTION MOLDS
Where: On horizontal and vertical injection molding machines.
When: Production of large batches.
Process: An injection molding machine automatically uploads the material. It is generally combined to Cartesian or anthropomorphic robots, or more simply to brushes that automatically remove the piece for an operator-free automated process.

COMPRESSION MOLDS
Where: On vertical compression molding machines.
When: Usually for small quantities, molding of expensive compounds, sampling batches with pilot molds, but also for finished products from niche markets calling for very high quality.
Process: The raw material is transferred manually by the operator on the under plate. When closing the molding machine, the material is compressed inside the cavities to shape the part.
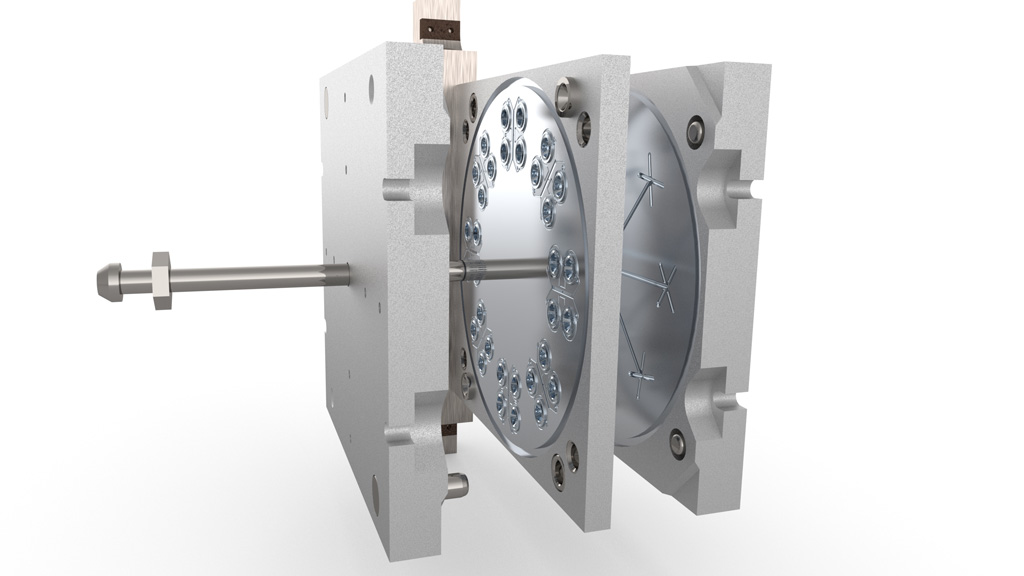
DOUBLE/SANDWICH MOLDS (3-PLATE INJECTION)
Where: On horizontal and vertical injection molding machines.
When: Production of large batches with twice the productivity.
Process: The central plate features cavities of both sides to obtain twice the productivity in a single cycle. The mold works automatically and is therefore the perfect solution for large productions. Available in two versions : with ejector or with springs.
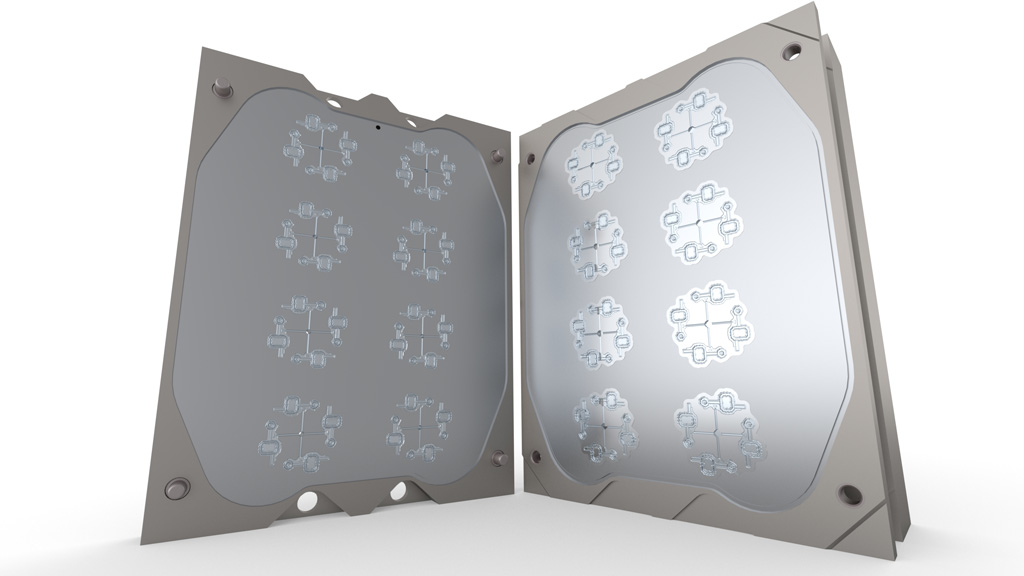
MULTI-NOZZLE MOLDS
Where: On horizontal and vertical injection molding machines.
When: Production of large and very large batches, often with very expensive compounds where saving on the runner material is essential both for quality and quantity.
Process: A cold-runner thermo-regulated block mounted on the molding machine plates enables to separate the incoming material flow, then special nozzles inject it directly into the profile or in zones very close to the cavity, thus greatly reducing the sprue material waste.
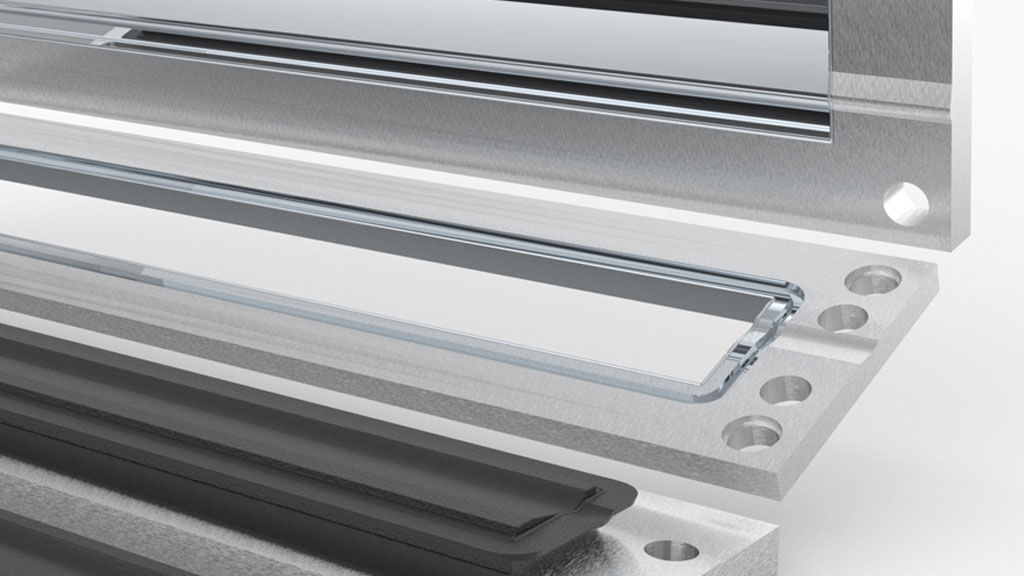
INJECTION COMPRESSION MOLDS (OR OPEN INJECTION)
Where: On vertical injection molding machines.
When: When the part design and characteristics call for it.
Process: Similar to compression molding, the only difference is that the compound is automatically injected when the mold is still open (about 10 mm). When the required quantity of compound is reached, the molding machine closes. It differs from injection molding as it doesn’t feature injection runners and film gates.
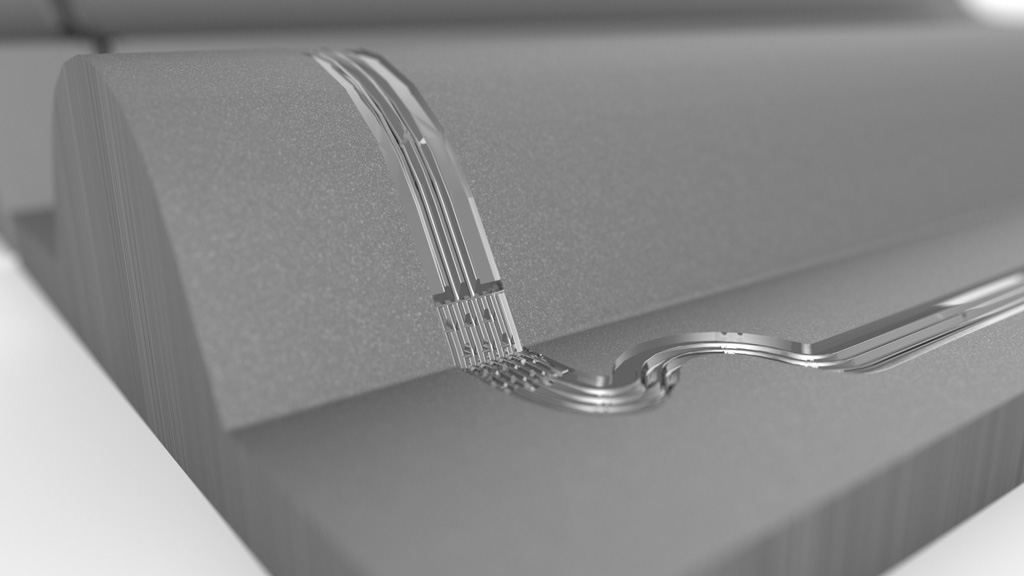
STAMPI TRANSFER
Where: On horizontal and vertical injection molding machines.
When: Ideal for thin membranes which require direct injection or injection in zones very close to cavity. The given advantages of this solution are : no outer flash on the rubber part and the mold does not suffer wear and tear.
Process: The feeding system is on plates 1 and 2 and it transfers the rubber directly in the cavities on plate 3 or very near.